Product Introduction
The intelligent composite robot Gemini mobile car integrates embedded, intelligent perception, SLAM, artificial intelligence, and machine vision technologies, supporting the rapid construction of various application scenarios such as logistics, inspection, intelligent picking, and composite AGV.

Product Features

Cargo Transport

Super Heavy Load

Ejector module

Transport module

Supporting Robot Arm

Multiple camera

Rich interfaces

Open source code

C++

Python

ROS

Use Tutorial

Designed Simulating Industrial AGV Structure
Gemini refers to the functionality, structure, and appearance design of real industrial AGV robots, scaled down in a 4:1 ratio, which is more suitable for teaching practice and simulating scenarios such as warehousing and logistics.
Compact body, surging power
A chassis with two wheel differential, four-wheel drive, and swing arm suspension can maintain flexible mobility even under load.


Highly Integrated Sensors
Highly integrated sensors such as LiDAR, depth camera, high-definition camera, ultrasound, etc. complement and work together to form a comprehensive and efficient perception system for robots.
Super Strong Computing Power
The Jetson series hosts not only ensure powerful computing power support, but also provide users with efficient data processing and intelligent decision-making capabilities.
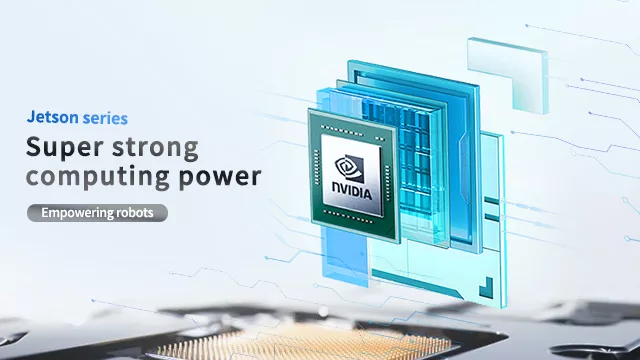

Rich Interfaces
Equipped with multiple power supply and communication interfaces, ensuring diversity in power supply and efficient data transmission. Equipment installation holes are reserved for users to install third-party devices, thereby achieving more unique functions and applications.
Status Display Light Bar, Touch Interactive Screen
The light bar can display the real-time running status of the robot, such as stationary, accelerating, emergency stop, turning, etc., providing users with intuitive feedback.

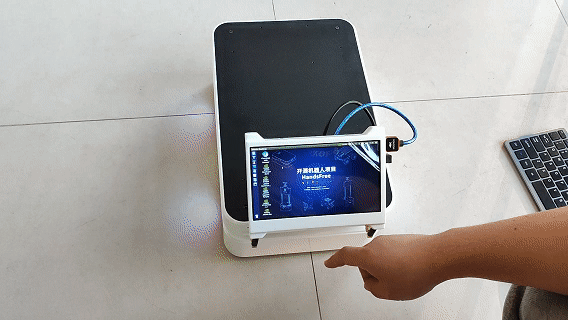
Touch Interactive Screen
The touch interactive screen supports multi touch, significantly improving the friendliness, efficiency, and convenience of user interaction. The open design of the touch interactive screen allows developers to easily customize and expand interface functions.
Designer and manufacturer of mobile robots, shipped to over 50 countries worldwide
Multiple kits for worry free expansion
Various expansion kits such as chassis expandable robotic arms, 4G remote driving, top lift modules, and transport modules provide a flexible learning platform for education and teaching through their diverse functional combinations. This allows students to exercise their skills in diverse practical scenarios and effectively enhance their ability to solve practical problems.

Collaborative Formation
The application of collaborative formation technology in education and teaching enables students to understand the working principles of multi-agent systems through practical operations, including key technologies such as communication protocols between agents, task allocation strategies, and dynamic formation maintenance, thereby enhancing students’ theoretical knowledge and practical skills in the fields of robotics engineering, automation, and artificial intelligence.

Kit collocation

Robot Arm Kit
Robot extension installation desktop six axis robotic arm. The effective working radius of the robotic arm is 280mm, the effective load at the end is 250g, and it can be equipped with mechanical claws.

Top Lifting Kit
The robot can be extended to install a lifting module, which can be used for cargo transportation and handling. The maximum weight that can be lifted is 2.5kg, with a stroke of 30mm.

Transport Module Kit
Robots can be extended to install transportation modules, which can be used for cargo transportation, simulating hotel meal delivery, and other scenarios.

Remote Driving Kit
The robot's expandable remote driving kit utilizes 4G/5G networks and deep learning technology to achieve remote control and problem detection in hazardous environments, ensuring the safety of workers.
Technical Parameter

Specification | Standard Configuration | High Configuration | |
Dimension | 350mmx235mmx140mm (about 13.77inx9.25inx5.51in) | ||
Ground Clearance | 12mm (about 0.47in) | ||
Driving Mode | 2 main wheels differential drive, 4 driven wheels with independent swing arm suspension | ||
Weight | 8kg | ||
Maximum Load | 20kg | ||
Maximum Speed | 0.65m/s (about 2.13ft/s) | ||
Maximum Climbing Angle | 25° | ||
Minimum Turning Radius | 0m | ||
Battery Capacity | 15000mAh | ||
Operating Time | 4h | ||
Standby Time | 8h | ||
Power Supply Interface | MR30,5V/12V(battery voltage) | ||
Communication Interface | SBUS、USB | ||
Embedded Host | Model number | Jetson Nano | |
CPU | Quad-core ARM® Cortex®-A57 MPCore Processor | ||
GPU | 128-core NVIDIA Maxwell™ architecture GPU | ||
Memory | 4GB | ||
Storage | 64GB | ||
AI performance | 472 GFLOPS | ||
Master Control | Master Chip | STM32 F3 series | |
Inertial Measurement Unit | Provide four element navigation information of pitch, roll, heading and rotation | ||
Lidar | Scanning Radius | 0.12-25m (about 0.39-82.02ft) | |
Accuracy | ±40mm (1.57in) | ||
Augular Resolution | 0.3° | ||
Scan Rate | 10Hz | ||
Sample Rate | 14000Hz | ||
Angular Range | 0-270° | ||
Depth Camera | RGB FOV | 71°x43.7° | |
RGB Resolution Framerate&Frame Rate | 1920*1080,30fps(Max) | ||
Depth FOV | 67.9°x45.3° | ||
Depth Resolution&Frame Rate | 640×400,30fps(Max) | ||
Depth Distance | 0.3~3m (about 0.98~9.84ft) | ||
Depth Accuracy | ±1-6mm (about 0.04-0.24in) (Within 1 meter) (about 3.28ft) | ||
HD Camera | Amount | 2 | |
Pixel | Eight million | ||
Resolution&Frame Rate | 1920×1080,30fps(Max) | ||
Ultrasonic sensor | Amount | 3 | |
Range | 2-450mm (about 0.07~17.72in) | ||
Accuracy | 0.5cm (about 0.2in) | ||
Frequency | 20Hz | ||
Screen | Resolution | 1024×600 | |
Dimension | 7in | ||
Touchscreen | Yes | ||
Speaker | Amount | 2 | |
Microphone | Amount | 2 | |
Interactive RGB | Show the real-time status of the car | ||
Ejector Module (optional) | Travelled Distance | / | 30mm (about 1.18in) |
Payload | / | 2.5kg | |
Transportation Module (optional) | Number of compartments | / | 4 |
