PRODUCT INTRODUCTION
The smart agricultural picking robot platform includes a mobile platform, a robotic arm, actuators, a vision system, and a control system. It supports autonomous navigation, intelligent obstacle avoidance, fruit and vegetable recognition, dynamic error calibration, and workload control, and can perform unmanned path planning and fixed-point parking.
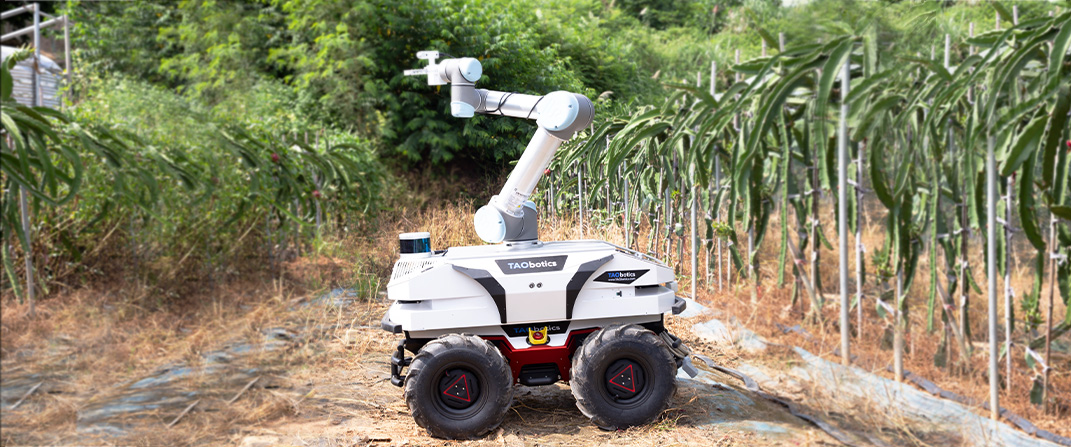
PRODUCT FEATURE
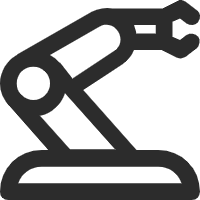
Supporting Robot Arm
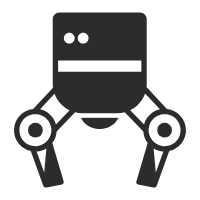
Visual Grab
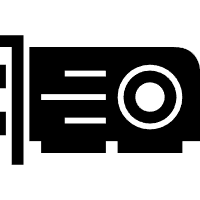
Strong Arithmetic Power
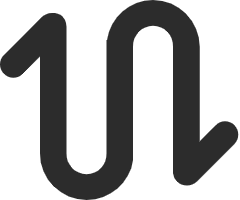
Autonomous Navigation
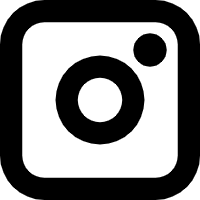
Depth Stereo Camera
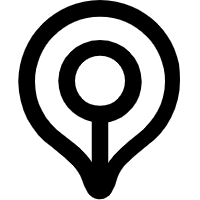
Lidar Positioning
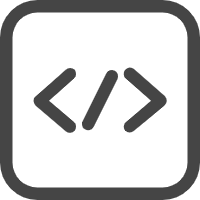
Secondary Development
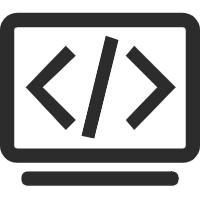
Open Source Code
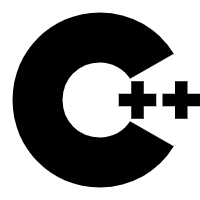
C++
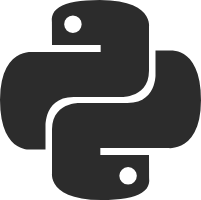
Python
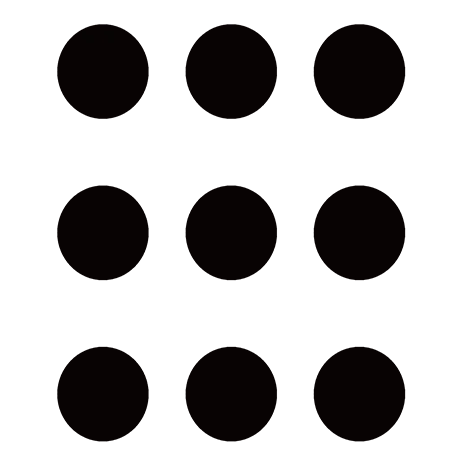
ROS
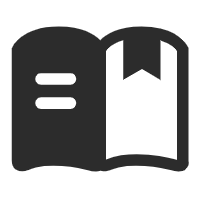
Use Tutorial
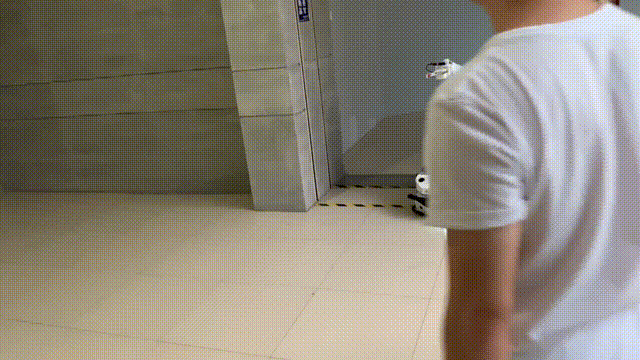
Real-Time Perception Obstacle Avoidance
Equipped with multiple advanced sensors, it accurately perceives the environment through fusion technology. The internal system utilizes advanced algorithms to process data, develop optimal obstacle avoidance strategies, achieve real-time obstacle recognition and safe path planning, and effectively reduce collision risks.
Hand-Eye Coordination
Equipped with depth cameras and advanced image processing algorithms to achieve fast target object recognition and localization. By combining precision robotic arms and flexible mechanical claws, flexible operation and stable grasping of target objects have been achieved.
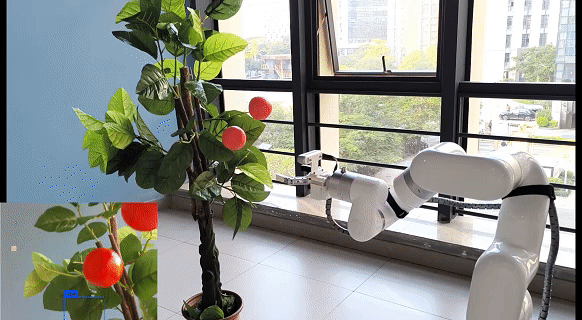
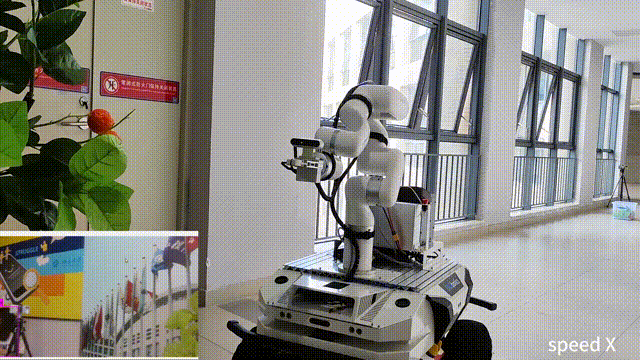
Automatically Identify Fruits and Vegetables
Integrating image recognition and artificial intelligence technology, robots capture and analyze fruit and vegetable images in real-time. Utilizing deep learning algorithms to quickly and accurately identify the types of fruits and vegetables, achieving efficient classification and processing.
Motion Planning of Robot Arm
Equipped with advanced robotic arm planning system, providing high precision and efficiency. The system utilizes complex algorithms and high-speed computing to finely plan each action, automatically adjust paths and speeds, adapt to different environments and task requirements, and ensure precise operation.
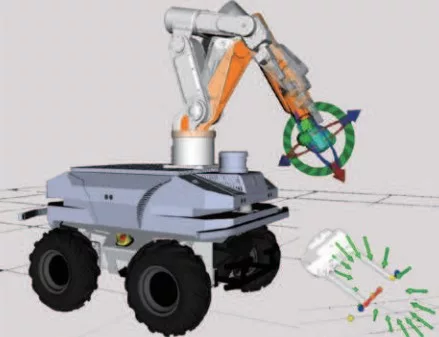
Designer and manufacturer of mobile robots, shipped to over 50 countries worldwide
RICH MATCHING SCHEMES
The platform integrates six intelligent unmanned vehicles and multiple robotic arms, supporting free combination according to research needs and simulating complex agricultural environments. Provide experimental support for research on precision agriculture, crop monitoring, and disease and pest identification.
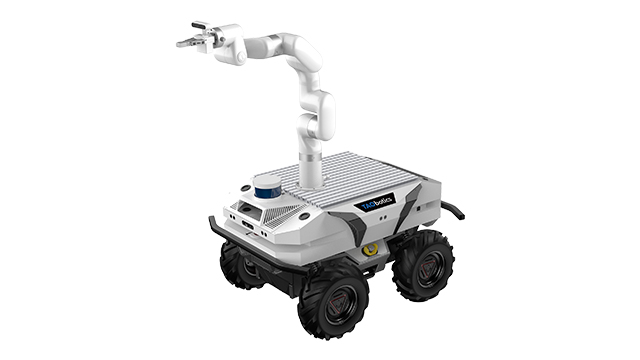
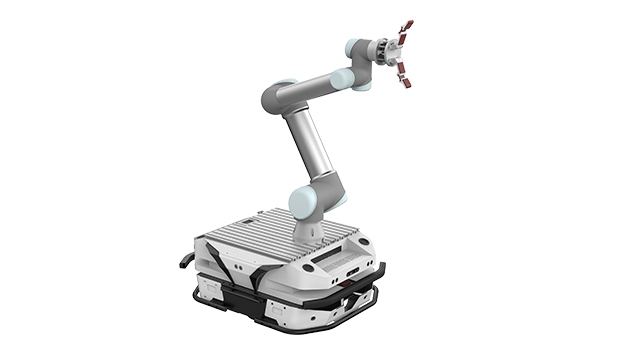
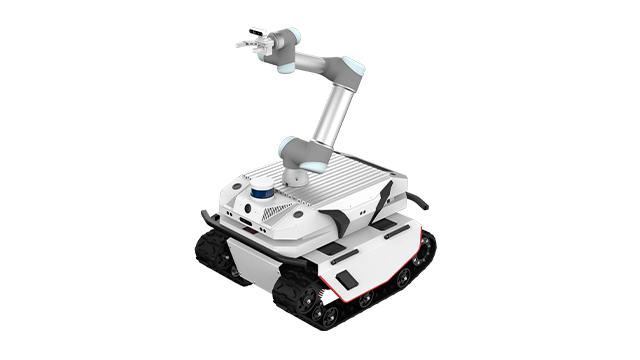
MODULAR DESIGN
Intelligent unmanned vehicles, collaborative robotic arms, and other agricultural intelligent devices can be selected and combined as independent modules. Modular design provides unprecedented flexibility and simplifies operation and maintenance processes.
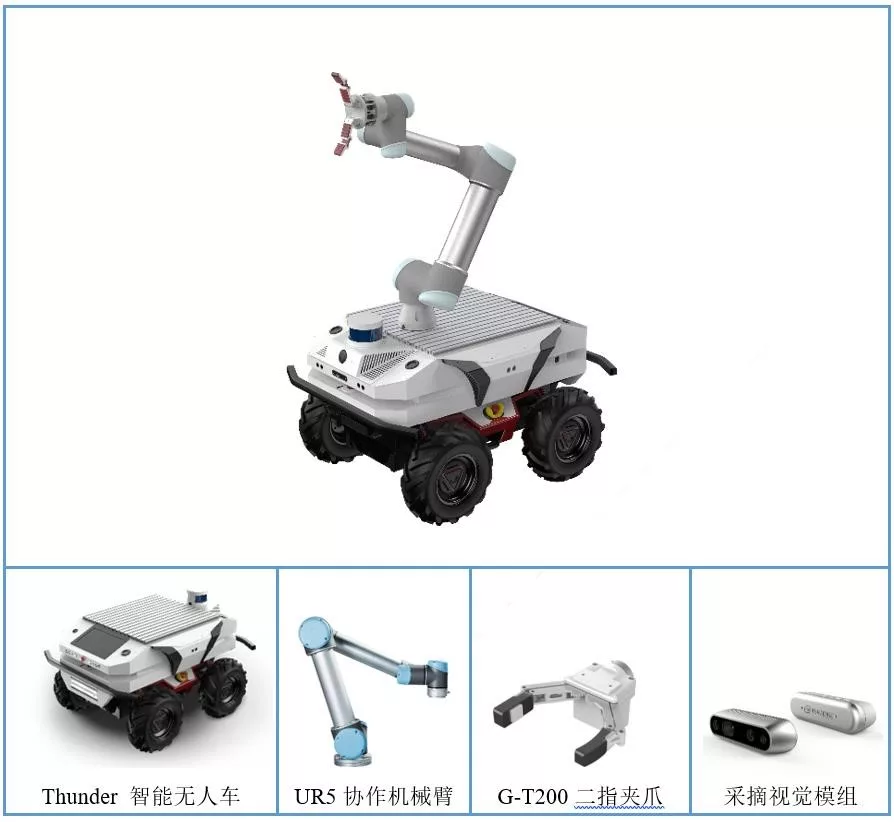
TECHNICAL PARANMETER
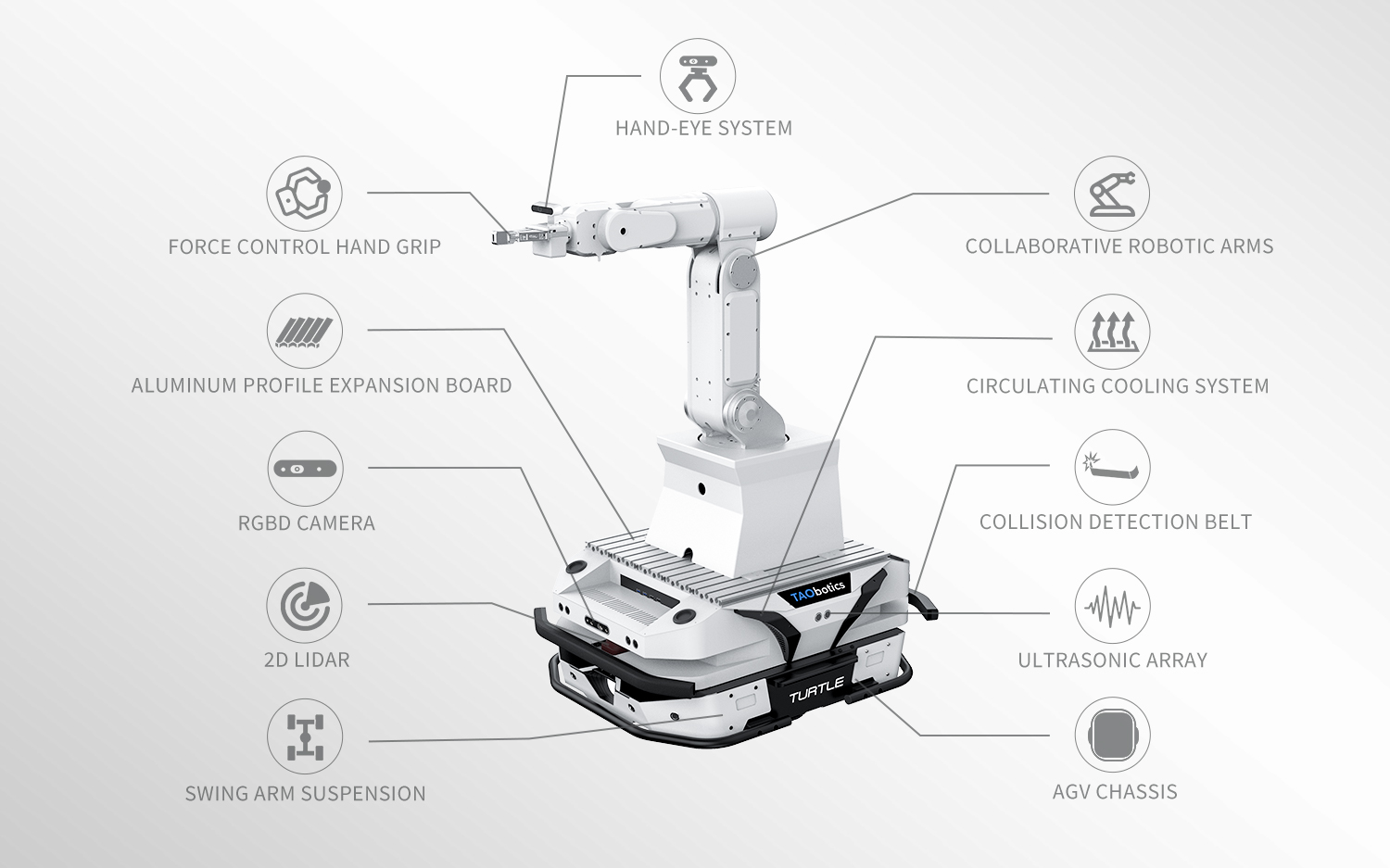
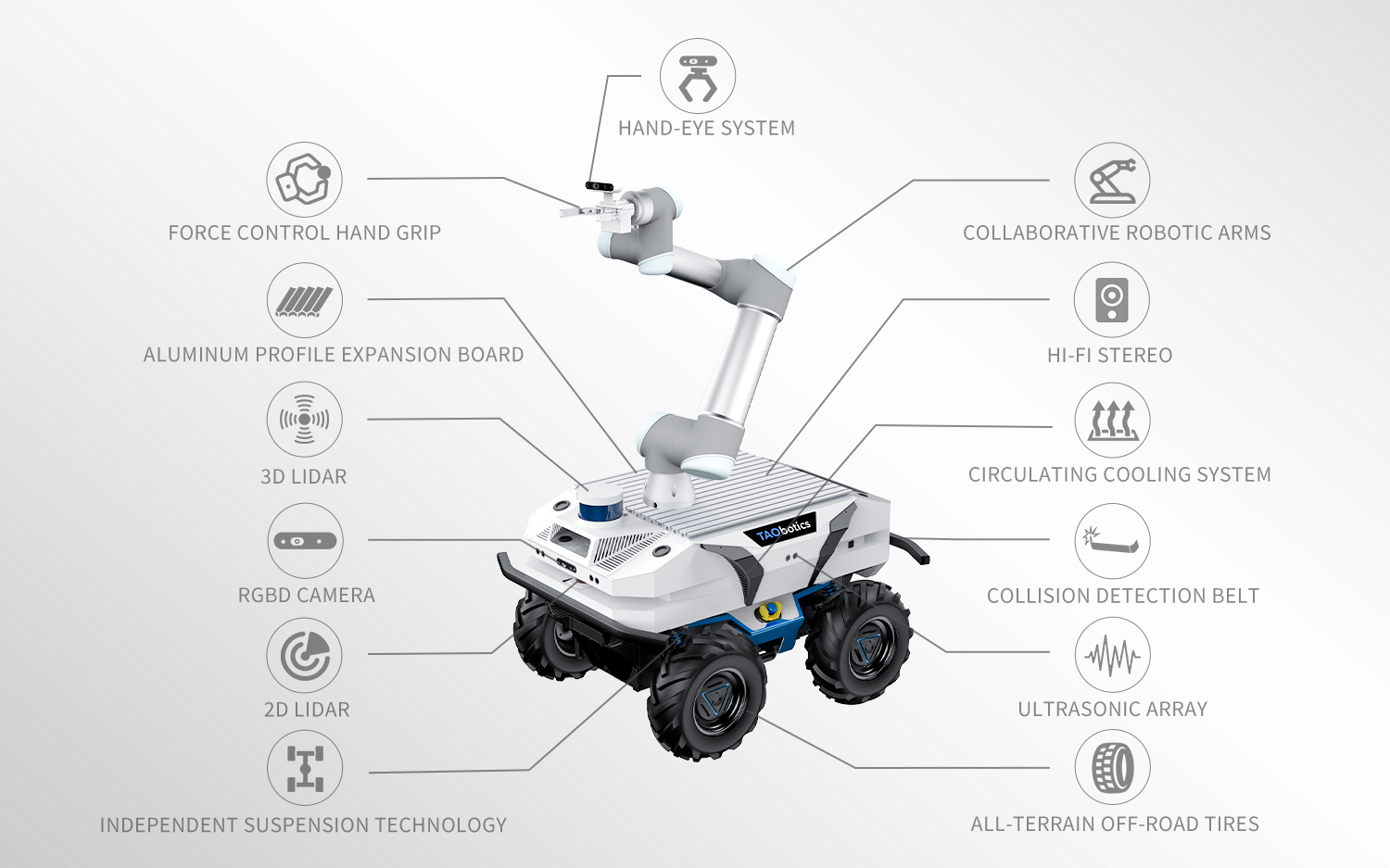
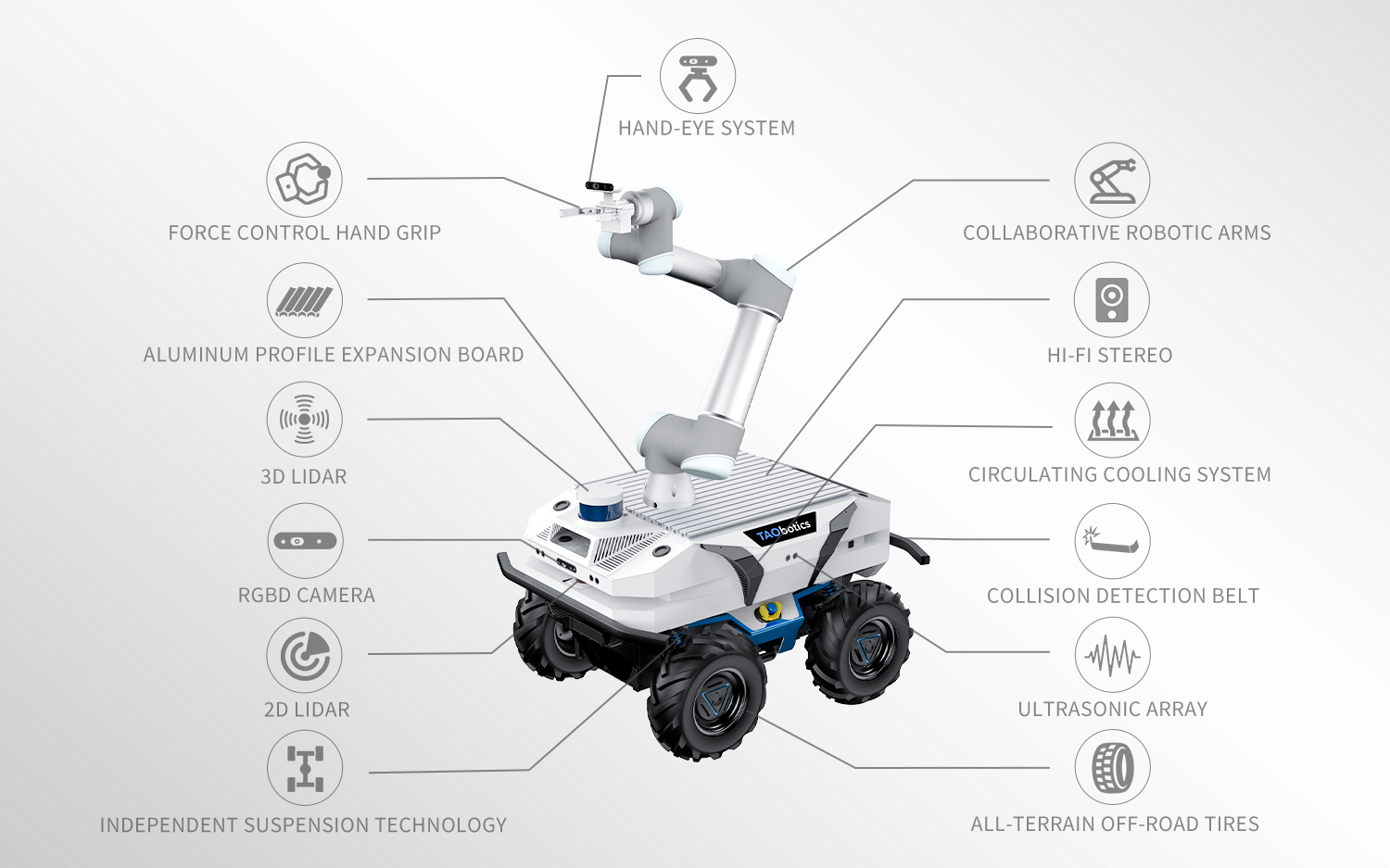
Specifications | Standard Configuration | Middle Configuration | High Configuration | |
Unmanned Vehicle | Intelligent Differential AGV Robot Standard configuration x1 | Intelligent Differential Four-wheel Drive Unmanned Vehicle High configuration x 1 | Intelligent Differential Four-wheel Drive Unmanned Vehicle High configuration x 2 | |
Robot Arm | Robot Arm Type | Intelligent Collaborative Robot Arm Kit V6_PLUS | Intelligent Collaborative Robot Arm Kit xArm6 | Intelligent Collaborative Robot Arm Kit UR5 |
Degree of Freedom | 6 | 6 | 6 | |
Weigh | 12.8kg | 12.2kg | 20.6 kg | |
Payload | 1500g | 5kg in maximum | 5 kg | |
Robot Arm Length | 660mm(about 25.98in) | 700mm(about 27.56in) | / | |
Reach | 600mm(about 23.62in) | 700mm(about 27.56in) | 850mm | |
Repeatability | 0.1mm(about 0.004in) | ±0.1mm(about 0.004in) | ±0.03mm | |
Maximum Speed at the End | 600mm/s(about 23.62in/s) | 1m/s(about 3.28ft) |
| |
Maximum Speed at the Joint | 1、2 axes 90º/s, 3、4 axes 120º/s, 5、6 axes 300º/s | 180º/s | 180°/s | |
Axis movement | 1axis [-150º,+150º], 2axis [-65º,110º], 3axis [-165º,+165º], 4axis [+25º,+185º], 5axis [-270º,270º], 6axis [-30º,+200º] | / | Base[-360º,+360º], Shoulder[-360º,+360º], Elbow[-360º,+360º], Wrist1[-360º,+360º], Wrist 2[-360º,+360º], Wrist 3[-360º,+360º]. | |
Power Supply | 24V/12A | / | / | |
Communication Interface | USB Communication Interface | TCP-IP/Enthernet | / |
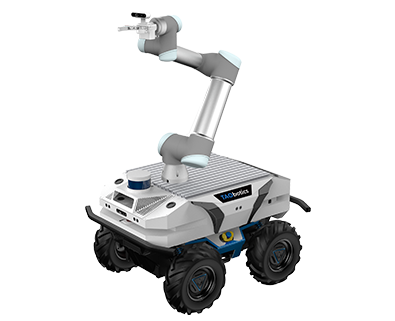